Classification of automatic control systems
Tabla de contenido
- Classification of automatic control systems
- Types Of Automatic Control Systems
- 1. Automatic Control Systems can be categorized into open-loop control, feedback control, and compound control based on the control method employed
- 2. Classification of Automatic Control Systems Based on Component Type: Mechanical, Electrical, Electromechanical, Hydraulic, Pneumatic, and Biological Systems
- 3. Classifying Automatic Control Systems Based on System Function: Temperature Control Systems, Pressure Control Systems, and Position Control Systems
- 4. Categorizing Automatic Control Systems based on System Performance: Linear and Nonlinear, Continuous and Discrete, Steady and Time-Varying, Deterministic and Uncertain Systems
- 5. Categorizing Automatic Control Systems Based on Input Quantity Change Rule: Constant Value Systems, Follow-Up Systems, and Program Control Systems
- 6. LiFePO4 Battery For Automatic Control Systems
- Experience the Best with Our Top-Rated LiFePO4 Battery – Get Yours Today!
- Más información sobre la batería
- Types Of Automatic Control Systems
Types Of Automatic Control Systems
1. Automatic Control Systems can be categorized into open-loop control, feedback control, and compound control based on the control method employed
Open-loop control:
In open-loop control, the system operates based on a predetermined set of instructions or commands without considering feedback. It is like following a recipe without checking if the dish is cooking properly.- Advantage: Open-loop control is simple and inexpensive to implement, making it suitable for systems where the output doesn't need to be precisely controlled.
- Disadvantage: It doesn't account for disturbances or changes in the system, so it may lead to errors and inaccuracies in the output.
Feedback control:
Feedback control continuously monitors the system's output and adjusts the input based on the feedback information. It is like driving a car while checking the rearview mirror to maintain a steady speed.- Advantage: Feedback control allows for error correction, adapts to changes in the system, and provides accurate and precise control.
- Disadvantage: It can be more complex and expensive to implement compared to open-loop control, as it requires sensors, feedback processing, and control algorithms.
- High Accuracy: Feedback control is known for its precise results.
- Stability Concerns: It can show slight signs of instability, like oscillations.
- Reduced Non-Linear Effects: Feedback control minimizes effects that are not straightforward.
- Less Impact from Outside Noises: Disturbances or external noises have reduced effects.
- Improved Product Quality: Using feedback control can lead to better product outcomes.
- Quick Response: Feedback control reacts quickly to changes in what it's trying to control.
- The input (what you start with),
- The process (what you're controlling),
- The output (the result),
- Sensors (they gather information),
- Controllers (they make decisions),
- Actuators (they take action).
- Sensors check the actual condition of what you're controlling.
- This information goes to the feedback controller.
- The controller compares the real condition to what it should be. The difference is called an error.
- If there's an error, the controller reacts by adjusting things to fix it.
- It sends signals to set things right according to the plan.
- If something unexpected changes the process, the sensors notice it and tell the controller.
Objectives of Feedback Control
- Ensuring Accurate Outcomes: The main goal of feedback control is to make sure that the system's output matches the desired result. It does this by following planned paths or staying close to target points.
- Resisting Disturbances: Feedback control works against disruptions that might change the output, enhancing the system's overall performance.
- Stabilizing Processes: It can also make unstable systems stable again.
- Amplifying Effects: In a positive feedback system, the controller adds the output values to the set points, aligning them with the input. This type of feedback can either amplify or diminish the action that triggered it, based on specific limits.
- Reducing Variations: Negative feedback occurs when the process's outcome influences its operation to minimize changes. This feedback fosters stability.
- Characteristics of Stability: Known for its stability, accuracy, and responsiveness, negative feedback subtracts the output from the input (desired value). The resulting difference is considered an error, showing how much the output deviates from the desired value.
- Advantages: Negative feedback stands out for its precise accuracy, reduced sensitivity to disturbances, its ability to smooth and filter, and its wide bandwidth.
- Responding to Errors: Feedback control focuses on minimizing errors after they occur.
- Handling Disturbances: Feedback control compensates for disturbances that impact the control variable, while feedforward control addresses disturbances before they can affect the control variable.
- Preventive vs. Reactive Approach: Feedback control springs into action only when there's a change in the control variable. In contrast, feedforward control takes preemptive steps.
- Predictive Actions: Feedforward control adopts predictive actions, unlike feedback control.
- Structural Differences: A feedforward control system includes a feedback mechanism, but a feedback control system typically does not incorporate feedforward elements.
- Disturbance Detection: Feedback control can detect all types of disturbances, a feature that feedforward control lacks.
- Adaptability and Versatility: Feedforward control is not suited for adaptable, non-linear, or time-varying systems, whereas feedback control does not have these limitations.
- Knowledge Requirements: Feedback control requires only a basic understanding of the process it controls, whereas feedforward control needs detailed information about the process.
Compound control:
Compound control combines elements of both open-loop and feedback control. It utilizes predefined instructions and incorporates feedback information to achieve the desired output. It is like following a recipe but tasting the dish along the way to make adjustments.- Advantage: Compound control offers the advantages of both open-loop and feedback control. It provides flexibility, adaptability, and improved accuracy in controlling systems.
- Disadvantage: Implementing compound control can be more complex and requires careful design and integration of open-loop and feedback control elements. It may also be more costly than individual control methods.
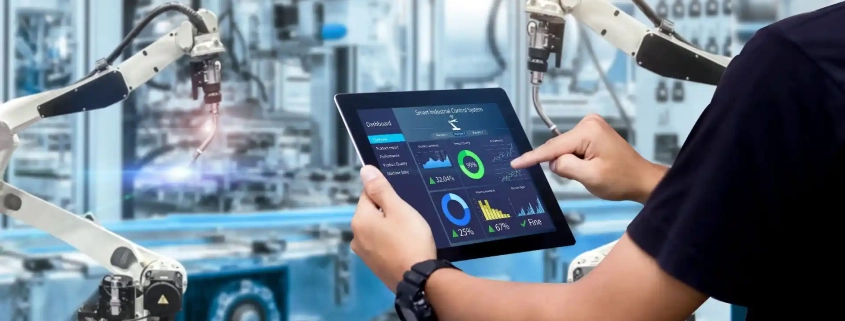
2. Classification of Automatic Control Systems Based on Component Type: Mechanical, Electrical, Electromechanical, Hydraulic, Pneumatic, and Biological Systems
Mechanical system:
A mechanical system is a collection of mechanical components that work together to perform a specific task, using physical forces and motion. It includes machines, gears, levers, and linkages.- Advantage: Mechanical systems are often durable, reliable, and have high power-to-weight ratios. They can handle heavy loads and operate in harsh environments.
- Disadvantage: They can be limited by their mechanical complexity and may require regular maintenance.
- Variable Air Volume (VAV) rooftop units
- Boiler/chiller systems
- Variable Refrigerant Flow (VRF) systems
- Air-source heat pumps
- Ground-source heat pumps
Electrical system:
An electrical system utilizes electrical components, such as wires, switches, and circuits, to control and transmit electrical energy for various applications.- Advantage: Electrical systems offer fast and precise control, high efficiency, and the ability to transmit power over long distances.
- Disadvantage: They can be sensitive to environmental conditions, require insulation and protection, and may pose safety hazards if not handled properly.
Electromechanical system:
An electromechanical system combines electrical and mechanical components to achieve specific tasks. It involves the conversion of electrical energy into mechanical motion and vice versa.- Advantage: Electromechanical systems offer the advantages of both electrical and mechanical systems, providing precise control, efficient energy conversion, and versatility in various applications.
- Disadvantage: They can be more complex and require careful integration of electrical and mechanical components, leading to increased costs and potential maintenance issues.
Hydraulic system:
A hydraulic system utilizes fluid, typically oil, to transmit and control power. It involves the use of pumps, valves, cylinders, and pipes to generate and control mechanical motion.- Advantage: Hydraulic systems can provide high forces and precise control, operate under high pressures, and are suitable for heavy-duty applications.
- Disadvantage: They can be prone to leaks, require regular maintenance of fluid levels and filtration, and are less efficient compared to some other systems.
Pneumatic system:
A pneumatic system uses compressed air to transmit and control power. It involves the use of compressors, valves, cylinders, and pipes to generate and control mechanical motion.- Advantage: Pneumatic systems are lightweight, easy to design and install, operate at high speeds, and are suitable for applications where cleanliness is important.
- Disadvantage: They typically provide lower forces compared to hydraulic systems, require a constant supply of compressed air, and may have limitations in terms of precision control.
- Air Compressor: The Starting Point The air compressor is the initial component of the system. It pulls in air from the environment and stores it by compressing and enclosing it in a specific space. A good example of a basic air compressor is a vacuum cleaner, which sucks in air along with dust and debris.
- Air Cylinders: Creating Movement Air cylinders are pivotal in transforming energy into mechanical force to drive the motor. They usually move in a straight line, but some models offer different types of movements. It's crucial to replace any damaged air cylinders to prevent irregular rotation that could harm the machine.
- Actuators: Controlling Valves Actuators play a critical role in opening and closing valves within the pneumatic system. They convert mechanical energy from pneumatic power to perform this task. Selecting the right actuators is important for efficient energy transfer.
- The Motor: The Driving Force The motor is the core component that operates when the cylinders move. Air motors vary in size and shape, tailored to the specific functions they are meant to perform.
- Reduced Fire Hazard: Unlike electrical systems, pneumatics use air, which poses no risk of electrical fires. This feature is particularly advantageous in environments dealing with flammable substances.
- Safe Gases: Pneumatic systems typically use regular air, primarily composed of oxygen and nitrogen. Even in case of leaks, the risk is minimal, unlike systems using flammable or scarce gases.
- Longevity and Low Maintenance: Pneumatic systems are durable and require less upkeep over time. Their operation without electricity or hydraulic fluids makes them less prone to damage.
- Versatility and Sustainability: Pneumatics are adaptable, powering both small and large machinery. Their potential as a renewable energy source is being explored, with initiatives to use compressed air for vehicles, aiming to reduce reliance on fossil fuels
Biological system:
A biological system refers to living organisms or parts of organisms that exhibit various functions and processes.- Advantage: Biological systems are highly adaptive, self-healing, and capable of complex and sophisticated functions.
- Disadvantage: They are subject to biological limitations, can be difficult to control externally, and may have ethical considerations in certain applications.
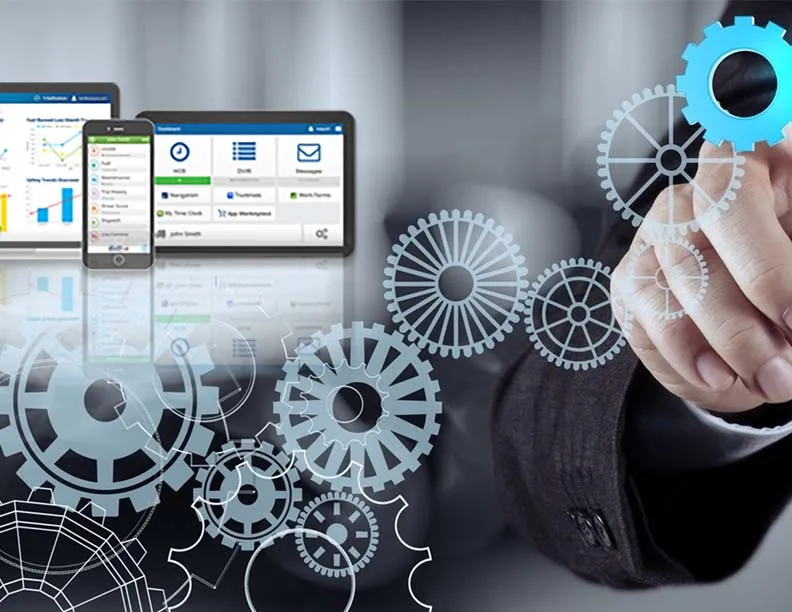
3. Classifying Automatic Control Systems Based on System Function: Temperature Control Systems, Pressure Control Systems, and Position Control Systems
Temperature control system:
A temperature control system is designed to regulate and maintain a desired temperature in a controlled environment or process. It involves sensors, actuators, and control algorithms to monitor and adjust the temperature.- Advantage: Temperature control systems enable precise regulation of temperature, ensuring optimal conditions for processes, comfort, and safety.
- Disadvantage: They can be sensitive to environmental changes, require accurate sensors, and may have limitations in terms of response time and energy efficiency.
Understanding Manual and Automatic Temperature ControlTemperature control is a vital aspect in many commercial processes to ensure the production of quality products. This control can be executed manually or via an automatic system.Manual Temperature Control: A Hands-On ApproachManual temperature control involves an operator who regularly checks the process temperature and adjusts the heating or cooling levels to maintain the desired temperature. This method is suitable for processes where small adjustments lead to gradual, minor changes.As depicted in the illustration, this approach is feasible for a limited number of processes with rare disturbances. However, manual temperature control demands a lot of attention and effort, as the operator needs to quickly respond to prevent temperatures from going beyond the acceptable range.Manual control is less favored in situations requiring high accuracy, multiple processes, or when temperature changes too swiftly for human intervention. In such cases, automatic control systems are the preferred choice, as they streamline processes and enhance efficiency.Automatic Temperature Control System: Enhanced Precision and EfficiencyIn an automatic temperature control system, the temperature (the controlled variable) is measured by sensors like thermocouples, RTDs, thermistors, or infra-red pyrometers. The sensor converts this temperature into a signal for the controller.The controller then compares this temperature reading to the set temperature (setpoint) and activates the final control device accordingly. This device adjusts the amount of heat added to or removed from the process by altering variables like air, water, steam, electricity, oil, or gas.Diverse Temperature Control DevicesThe final control elements in these systems include contactors, blowers, motor or pneumatic dampers and valves, motor-operated variacs, and various SCR’s and reactors.When selecting an automatic temperature controller, it's crucial to consider:
- The specific characteristics of the process
- The acceptable range of temperature deviation from the setpoint
- The optimal controller type for the process and its precise tuning
Pressure control system:
A pressure control system is used to maintain a specific pressure level within a system or process. It includes pressure sensors, valves, and controllers to monitor and adjust the pressure.- Advantage: Pressure control systems ensure stability and safety by preventing overpressure or underpressure situations, protecting equipment and ensuring consistent performance.
- Disadvantage: They may require careful calibration, regular maintenance, and can be affected by variations in load or system dynamics.
Position control system:
A position control system is employed to achieve and maintain a specific position or movement of a mechanical system or component. It utilizes sensors, actuators, and control algorithms to monitor and adjust the position.- Advantage: Position control systems allow for precise positioning, accurate movement control, and can be used in applications such as robotics, manufacturing, and automation.
- Disadvantage: They can be influenced by factors like friction, backlash, and mechanical wear, requiring compensation and periodic calibration.
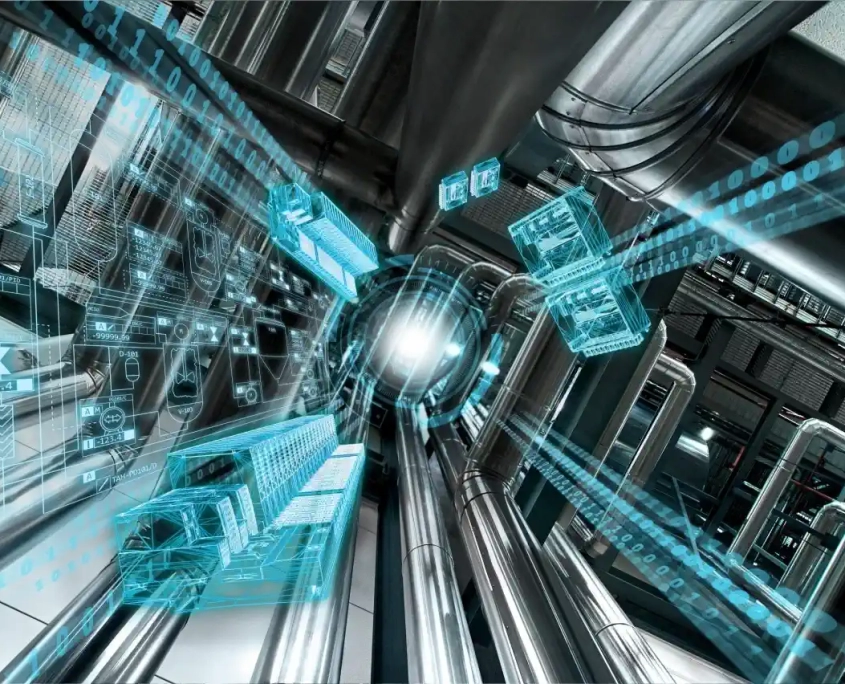
4. Categorizing Automatic Control Systems based on System Performance: Linear and Nonlinear, Continuous and Discrete, Steady and Time-Varying, Deterministic and Uncertain Systems
Linear system:
A linear system is a system that follows the principle of superposition, where the output is directly proportional to the input. The relationship between input and output can be described by linear equations or functions.- Advantage: Linear systems are relatively straightforward to analyze and control. They have well-defined mathematical properties and can often be solved analytically.
- Disadvantage: Linear systems may not accurately model complex real-world phenomena, as many systems exhibit nonlinear behavior.
- Engineering and Physics: In engineering (mechanical, electrical, civil) and physics, linear systems help in analyzing forces, predicting movements, and designing control systems.
- Economics and Finance: In economics, they model production or pricing strategies, while in finance, they assist in analyzing and optimizing stocks and investment strategies.
- Computer Science and Programming: Linear systems are instrumental in computer science for machine learning, cryptography, and developing optimization algorithms. They help in pattern analysis and improving algorithm performance.
Nonlinear system:
A nonlinear system is a system where the output is not directly proportional to the input. The relationship between input and output is described by nonlinear equations or functions.- Advantage: Nonlinear systems can represent a wide range of real-world phenomena with greater accuracy, capturing complex dynamics and behaviors.
- Disadvantage: Analyzing and controlling nonlinear systems can be more challenging, often requiring numerical methods or approximations.
Continuous system:
A continuous system is a system where the input and output variables are defined and measured over a continuous range of time or space.- Advantage: Continuous systems allow for precise modeling and analysis of phenomena that occur smoothly and continuously.
- Disadvantage: Implementing continuous systems may require specialized hardware and sophisticated control algorithms.
Discrete system:
A discrete system is a system where the input and output variables are defined and measured at specific points in time or space.- Advantage: Discrete systems are easier to implement and analyze, as they can be represented by sequences of values.
- Disadvantage: Discrete systems may not accurately represent phenomena that occur continuously or have rapidly changing dynamics.
Steady system:
A steady system is a system where the output remains constant over time, despite changes in the input.- Advantage: Steady systems offer stability and predictability, making them suitable for applications where constant output is desired.
- Disadvantage: Steady systems may not be able to adapt to changing conditions or respond to dynamic inputs.
Time-varying system:
A time-varying system is a system where the output changes over time, even with a constant input.- Advantage: Time-varying systems can capture dynamic behavior and adapt to changing conditions.
- Disadvantage: Analyzing and controlling time-varying systems can be more complex and may require real-time monitoring and adjustment.
Deterministic system:
A deterministic system is a system where the output is entirely predictable based on the input, following specific rules or equations.- Advantage: Deterministic systems allow for precise analysis and control, as their behavior is entirely defined by known relationships.
- Disadvantage: Deterministic systems may not account for uncertainties and variations present in real-world scenarios.
- Clear Rules: In deterministic systems, the guidelines are explicitly clear and leave no space for different interpretations.
- Consistent Outcomes: For any given input, these systems consistently produce the same output, no matter who is performing the calculation.
- Absence of Randomness: These systems don't include any elements of chance or unpredictable processes. Every action and outcome in a deterministic system is pre-determined and follows specific rules.
- Predictability: The nature of deterministic systems allows us to accurately forecast their future behavior.
- Newton's Laws of Motion: These laws provide a deterministic framework for predicting the movement of objects. Knowing an object's initial speed and location, we can determine its exact position at any future point.
- MySQL Databases: These databases operate deterministically. Supplying the same data input always results in identical output.
- Weather Prediction Models: Despite the complexity of weather patterns, the models for forecasting are fundamentally deterministic. By examining different atmospheric conditions, meteorologists can make precise weather forecasts.
- Electronic Circuit Functionality: The operation of electronic circuits is deterministic. Engineers can predict how a circuit will perform by studying its components and the flow of electricity.
- Game Strategy Theories: Games like chess and checkers operate under deterministic principles. The game rules clearly define permissible moves and their outcomes.
Uncertain system:
An uncertain system is a system where the output is influenced by random or uncertain factors, making it difficult to predict or control precisely.- Advantage: Uncertain systems can model real-world scenarios with inherent variability and uncertainties.
- Disadvantage: Uncertain systems pose challenges in analysis and control, as they require probabilistic or statistical approaches to account for uncertainty.
5. Categorizing Automatic Control Systems Based on Input Quantity Change Rule: Constant Value Systems, Follow-Up Systems, and Program Control Systems
Constant value system:
A constant value system is a system where the output remains fixed and does not change regardless of the input or other factors. It maintains a constant output value.- Advantage: Constant value systems are simple to implement and can provide a consistent and predetermined output.
- Disadvantage: They lack adaptability and responsiveness to varying inputs or changing conditions, limiting their usefulness in dynamic environments.
Follow-up system:
A follow-up system is a control system that adjusts the output based on the input, aiming to closely follow or track the input signal. It attempts to mirror or replicate the input as accurately as possible.- Advantage: Follow-up systems allow for precise tracking and replication of desired input signals, making them suitable for applications requiring accurate reproduction.
- Disadvantage: Follow-up systems may be sensitive to disturbances or noise in the input, leading to potential errors or inaccuracies in the output.
Program control system:
A program control system is a system that operates based on a predefined program or set of instructions. It follows a predetermined sequence of actions or commands to achieve a desired outcome.- Advantage: Program control systems provide a structured and repeatable approach to control, allowing for automation and consistent performance.
- Disadvantage: They may lack adaptability or flexibility, as they are limited to the predefined program and may not respond well to unexpected or dynamic situations.
6. LiFePO4 Battery For Automatic Control Systems
LiFePO4 batteries are a type of rechargeable battery that has established its place as a trusted power solution for automatic control systems. They're produced by numerous manufacturers, each offering unique advantages. One renowned manufacturer that stands out from is MANLY Battery.MANLY Battery is a professional LiFePO4 proveedor de baterías. It is known for its advanced technology and high-quality batteries. They have effectively harnessed the potential of LiFePO4 to create batteries that deliver impressive performance and longevity. MANLY 12 volt lithium battrery is the best selling product for automatic contraol systmes. Now, let's delve further into the distinct features and advantages of LiFePO4 battery that make them so beneficial for various control applications.
Experience the Best with Our Top-Rated LiFePO4 Battery – Get Yours Today!
Upgrade Your Golf Cart with MANLY's 12V 100Ah LiFePO4 Lithium Battery
Step into a world of robust power with our 12V 100Ah LiFePO4 battery, not just a powerhouse for golf carts but a versatile solution for a wide range of applications. This 100ah lithium battery is designed to meet the high-energy demands of various settings, ensuring that you have reliable, long-lasting power wherever you need it.Beyond the fairways, this LiFePO4 battery 100ah unit is perfect for a multitude of other uses. It's an ideal choice for off-grid solar energy systems, providing dependable storage for solar power. Homeowners and adventurers alike can rely on this battery for RVs and caravans, ensuring comfortable and uninterrupted power supply during travels. It's also well-suited for marine applications, like powering boats and yachts, where consistent and durable energy is essential.For those in the industrial sector, the 12v 100ah LiFePO4 battery offers a steadfast power source for heavy-duty equipment and backup systems, ensuring operations continue smoothly without power interruptions.
- Wide Application Range: From golf carts to solar systems, RVs, marine, and industrial equipment, this battery adapts to various power needs.
- Low Self-Discharge Rate: Retains most of its charge for extended periods, with a minimal monthly discharge, making it perfect for seasonal or occasional use.
- Smart Technology Integration: Features like optional Bluetooth connectivity and a battery level display enhance user convenience across applications.
- Extreme Durability: Operates reliably in a wide temperature range, making it suitable for outdoor and challenging environments.
- Long-Term Warranty: A 10-year warranty backs this battery, reflecting our commitment to quality and customer satisfaction.
- Enhanced Safety Features: Equipped with protection against short circuits, overcharging, and over-discharging, ensuring safety across all its applications.
Experience Unmatched Power with the 200Ah Lithium Battery
Unleash the full potential of your golf cart with our high-capacity 12V 200Ah LiFePO4 battery. Engineered to meet the rigorous demands of golf courses, this 200ah lithium battery is a powerhouse, offering enough endurance to easily handle over 18 holes of golf. This ensures a full day of play without the inconvenience of mid-day recharging. When it does come time to recharge, the process is efficient, typically taking only 6 to 12 hours depending on your charger's power output, making these lithium batteries 200ah a reliable and long-lasting energy solution for your golf cart.Perfect for those who value consistent performance and uninterrupted play, the 12v 200ah LiFePO4 battery combines convenience with robust power.
- Low Self-Discharge Rate: Retains over two-thirds of its charge for a year, with a minimal monthly discharge rate of 2.5% at 77℉, ensuring readiness for use.
- Smart Technology Integration: Offers optional Bluetooth connectivity and an easily accessible battery level display for user convenience.
- Built for Tough Conditions: Excellently suited for challenging environments, functioning reliably in temperatures ranging from -20°F to +150°F. Includes safety measures for extreme temperatures.
- Solid Warranty Assurance: Your investment is secured with a 10-year warranty, reflecting our confidence in the battery's longevity and performance.
- Enhanced Safety Features: Comes equipped with comprehensive safety protocols, including short circuit, overcharge, and over-discharge protection. The balanced circuit design allows safe connection of multiple batteries in series or parallel.
Introducing the 12 Volt 20Ah Lithium Battery - A Versatile Power Solution
Elevate your power game with our 12 Volt 20Ah Lithium Battery, a versatile and robust energy source suitable for a myriad of applications. This compact yet powerful battery is designed to cater to various needs, from small-scale solar power systems to essential backup for critical devices.The 12 volt 20ah lithium battery is not just about delivering power; it's about doing so efficiently and reliably. It's an excellent choice for outdoor enthusiasts needing a dependable power source for camping gear, as well as homeowners looking to enhance their solar energy setups. Its compatibility with solar panels makes it an eco-friendly option, providing a sustainable way to store and use solar energy.One of the standout applications of this battery is in the realm of automatic control systems. Its reliable and consistent power output makes the 12 volt 20ah battery a suitable choice for various automatic control systems. These systems require consistent and uninterrupted power to function effectively, and this battery is up to the task. Whether it's for home automation, industrial control systems, or other applications where stable power is crucial, this battery delivers.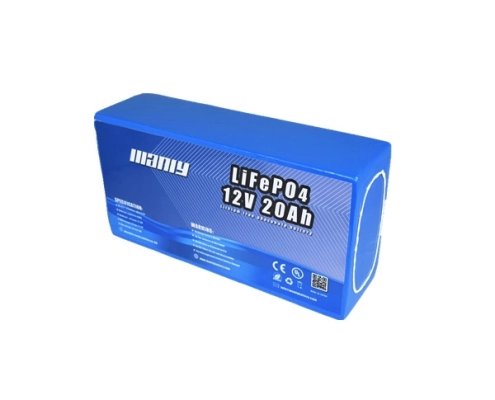
Características clave:
- Eco-Friendly and Efficient: Perfect for solar-powered setups, offering a sustainable energy solution.
- Compact and Lightweight: Its design makes it easy to install and transport, ideal for both stationary and portable applications.
- Durable and Long-Lasting: With lithium technology, expect a longer lifespan and consistent performance over time.