2024 Combien coûte une batterie de chariot élévateur
Table des matières
- 2024 Combien coûte une batterie de chariot élévateur
- Le coût réel des batteries de chariot élévateur au plomb
- Le coût réel des batteries de chariot élévateur au lithium
- 1. Coût de la batterie au lithium pour chariot élévateur
- Tableau du coût de la batterie de chariot élévateur au lithium MANLY (liste partielle) :
- 2. Sécurité de la batterie du chariot élévateur au lithium-ion
- 3. Avantages des batteries lithium-ion sur le marché des chariots élévateurs
- 4. Productivité améliorée
- 5. Stimuler la compétitivité opérationnelle
- Comment évaluer si le lithium-ion convient à votre flotte
- Étapes pour convertir votre flotte de chariots élévateurs aux batteries au lithium
- 1. Évaluez votre flotte actuelle de chariots élévateurs
- 2. Choisissez la bonne batterie au lithium
- 3. Tenez compte du poids et de l’équilibre
- 4. Améliorez ou ajustez l'équipement de charge
- 5. Former les opérateurs sur la recharge d’opportunité
- 6. Installer des systèmes de surveillance et de sécurité
- 7. Évaluez le coût total de la conversion
- 8. Envisagez une expansion future
- Conclusion
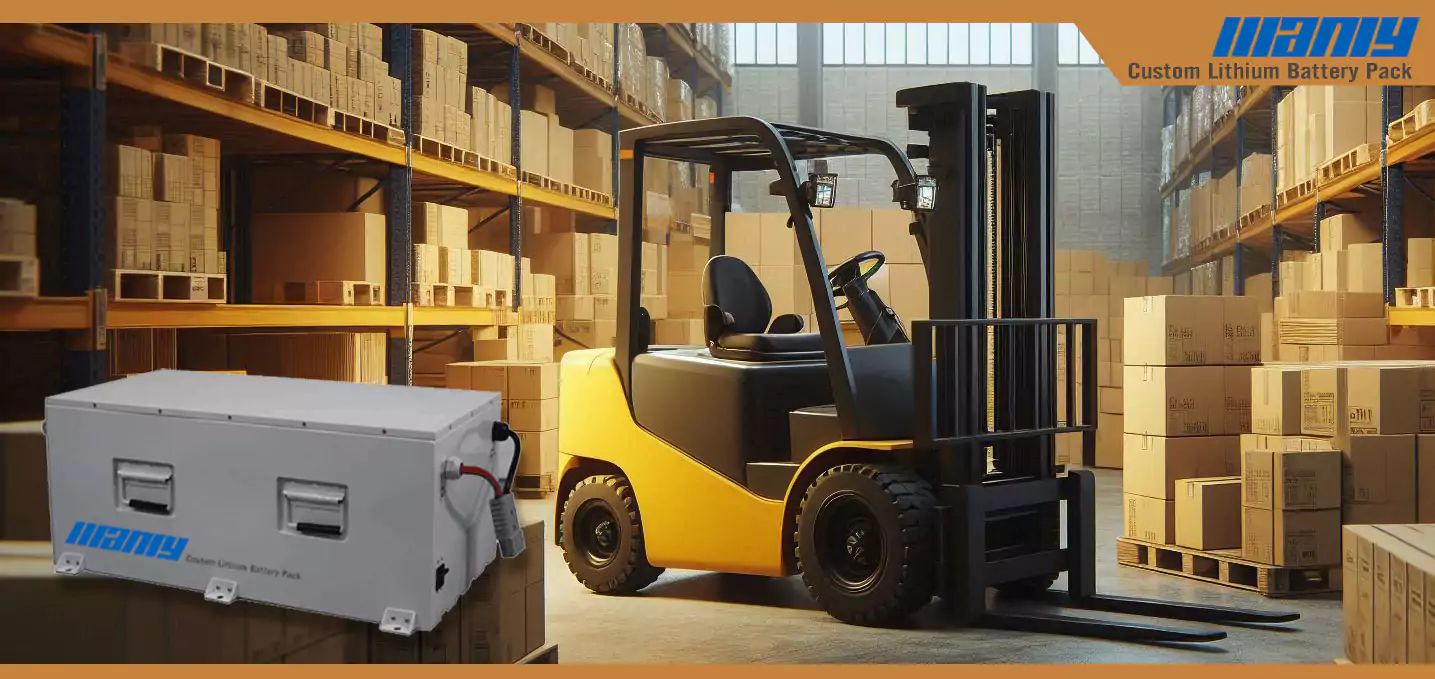
Le coût réel des batteries de chariot élévateur au plomb
1. Coût des batteries au plomb au fil du temps
The initial cost of a lead acid forklift battery might seem appealing due to its lower upfront price compared to lithium alternatives. However, the real expense accumulates over time due to several factors related to performance, labor, and operational efficiency. Lead-acid batteries typically require extensive maintenance, including regular watering, equalizing charges, and frequent monitoring. These processes consume both time and resources.Each lead acid forklift battery can only operate for about 8 hours before needing a recharge, which takes approximately 16 hours to fully charge and cool down. For warehouses that run 24-hour operations, this means each forklift needs at least three batteries to function continuously. Managing these batteries requires labor-intensive tasks, such as switching out batteries, monitoring charging cycles, and performing maintenance, which leads to increased labor costs over time. The need to frequently stop operations to change batteries also reduces overall productivity, making the long-term cost of lead-acid batteries higher than initially perceived.Over time, forklift battery replacement becomes inevitable as lead-acid batteries lose efficiency after around 1500 charge cycles, which generally occurs every 2-3 years. This frequent replacement cycle, combined with the need for multiple batteries per forklift, drives up costs significantly compared to alternatives like lithium forklift batteries, which have much longer lifespans and quicker charging times.2. Coûts de stockage des batteries au plomb
One often overlooked cost associated with lead acid forklift battery use is the storage requirement. Lead-acid batteries are large and bulky, and warehouses must dedicate considerable space for both storage and charging stations. These batteries need a specific area for safe charging and cooling, often referred to as the battery room, which must meet strict guidelines to ensure safety.The battery storage area must have proper ventilation to manage the gases emitted during the charging process, as well as the necessary infrastructure to handle these heavy batteries. This involves installing equipment such as overhead cranes or battery transfer carts to move the batteries safely. In addition to the physical space required, warehouses must invest in specialized monitoring systems to track battery conditions, charging cycles, and maintenance needs, all of which increase operational costs.The storage area cannot be repurposed for other productive uses, meaning that valuable warehouse space is taken up solely for battery management. Over time, the inefficiency in space usage contributes to increased costs, particularly for businesses looking to maximize their warehouse floor for inventory or other operational needs.3. Risques et dangers professionnels
The use of lead acid forklift batteries also introduces significant occupational hazards. These batteries contain corrosive sulfuric acid and lead, both of which pose serious risks to workers. If a battery leaks or spills, it can cause severe chemical burns or environmental contamination. Handling these batteries requires specialized safety equipment and training to avoid accidents, adding to the operational cost.Moreover, during the charging process, lead-acid batteries emit hydrogen gas, which is highly flammable. This creates a potential explosion risk if the gas accumulates in an inadequately ventilated space. Battery charging areas must be equipped with proper ventilation systems and safety measures to mitigate these risks. Even with these precautions, the possibility of accidents remains, which can lead to costly downtime, medical expenses, and potential fines if workplace safety regulations are not strictly followed.In addition to physical risks, the labor required to maintain lead-acid batteries is another source of long-term cost. Workers must regularly water the batteries, clean corrosion from the terminals, and ensure that they are properly charged and cooled. These maintenance tasks take time away from other productive activities, adding hidden costs to the overall expense of using lead-acid batteries.4. Frais de remplacement des batteries au plomb
Forklift battery replacement is a recurring cost that companies using lead-acid batteries must factor into their long-term budgeting. As mentioned earlier, these batteries typically last around 1500 charging cycles, which translates to about 2-3 years of usage under normal conditions. After this period, they need to be replaced, and this can become quite expensive when managing a large fleet of forklifts.Each lead acid forklift battery is a significant investment, and purchasing multiple batteries every few years adds up. The cost of disposal also needs to be considered, as lead-acid batteries contain hazardous materials that require proper handling and recycling. Failing to dispose of them correctly can result in fines or environmental penalties, adding to the overall expense.In contrast, lithium forklift batteries offer a much longer lifespan, often lasting up to 5000 cycles, which significantly reduces the frequency of replacement. While the upfront cost of lithium batteries is higher, the long-term savings in replacement expenses, maintenance, and labor make them a more cost-effective option for many businesses.Le coût réel des batteries de chariot élévateur au lithium
1. Coût de la batterie au lithium pour chariot élévateur
When comparing the costs of batteries de chariot élévateur au lithium to lead-acid alternatives, the upfront price is significantly higher. On average, a lithium forklift battery costs between $17,000 and $20,000, which is about 2 to 2.5 times the price of a comparable lead-acid battery. This higher initial cost can be a deterrent for some businesses, but it’s essential to consider the long-term savings that come with this investment.The primary areas where lithium forklift batteries save costs include energy efficiency, reduced downtime, minimal maintenance, and longer lifespan. Lithium forklift batteries are about 30% more energy-efficient than lead-acid batteries, and they can charge up to eight times faster. This means less electricity is used to power the same amount of work, leading to noticeable savings on energy bills over time. Additionally, the ability to charge the battery during breaks ensures continuous operation, which eliminates the need for multiple batteries per forklift, reducing overall battery investment.Moreover, lithium forklift batteries can last two to four times longer than lead-acid batteries, meaning fewer replacements are needed over the years. This extended lifespan reduces the total number of batteries that need to be purchased, stored, and maintained, which further lowers overall operational costs. Although the initial lithium forklift battery cost is higher, the total cost of ownership becomes more favorable as savings accumulate in energy, labor, and replacements.In addition to the general price range of lithium forklift batteries, MANLY Battery offers a more accessible option for businesses of all sizes. MANLY's lithium forklift battery range is priced between $250 and $7,500, depending on the forklift model and battery capacity. This competitive pricing ensures that companies looking to switch to lithium technology have a broader range of options, from smaller forklifts requiring less power to larger industrial models. MANLY Battery's products maintain high performance and durability while offering a more cost-effective solution in the lithium forklift battery market, making it easier for businesses to transition without the steep initial investment often associated with lithium technology.Tableau du coût de la batterie de chariot élévateur au lithium MANLY (liste partielle) :
Numéro de modèle | spécification | Prix unitaire (USD) | Remarques |
≤200 | |||
MLP24150M | Battery Type: LiFePO4 Nominal Voltage:25.6V; Rated Capacity: 150AH Steel Case; Dimension: 640*245*220mm Cycle life: 5,000+ times; Lifespan: 15+ years design | $750.00 | Le prix EXW par batterie exclut les frais supplémentaires |
MLP36200M | Battery Type: LiFePO4 Nominal Voltage: 38.4V; Rated Capacity: 200AH Steel Case; Dimension: 560*520*180mm Cycle life: 5,000+ times; Lifespan: 15+ years design | 1 500,00 $ | |
MLP72420M | Battery Type: LiFePO4 Nominal Voltage: 73.6V; Rated Capacity: 420AH Steel Case; Dimension: 700*600*550mm Cycle life: 5,000+ times; Lifespan: 15+ years design | 6 000,00 $ |