Future Tech: Innovations in Lithium Ion Battery Separator
Table of Contents
What is Separator in Lithium Ion Battery
The separator is one of the four key materials in a lithium-ion battery. It's like the heart of the battery. The separator acts as both an insulator and a semi-permeable layer. Why is it important? Well, it does two main things:- First, it keeps the battery safe. The separator makes sure the positive and negative ends of the battery don’t touch. This helps avoid any short circuits.
- Second, the separator helps the battery work right. When you charge or use the battery, lithium ions move through tiny holes in the separator. This separator is a thin sheet with lots of super-small holes. These holes need to be just the right size: big enough for the lithium ions to move but small enough to block any electric flow. This way, the battery can charge and work correctly.

How to Make a Lithium Ion Battery Separator
There are two main methods to make lithium-ion battery separators: the dry process and the wet process.Starting with the dry method, there are two techniques. One is the single-stretch, and the other is the double-stretch. The double-stretch technique was developed by the Chinese Academy of Sciences' Institute of Chemistry. However, it's not widely used now because it didn’t meet the performance standards people wanted. The equipment for the dry process is pretty reliable, and the whole thing is pretty straightforward. One big advantage is that the dry method doesn't have much heat shrinkage, so it's safer. Plus, it's cheaper. This makes it great for making separators for storage batteries, consumer batteries, and iron phosphate lithium power batteries.On the other hand, the wet method costs more than the dry one. But it has its perks. The separators made with the wet process have uniform and well-aired holes. They can also be thinner and lighter. Many think that "wet-base + coated layer" separators are best for high-energy-density power batteries. Right now, the wet method is leading the way. More separators are made using the wet process than the dry one, and it's the go-to choice in the market.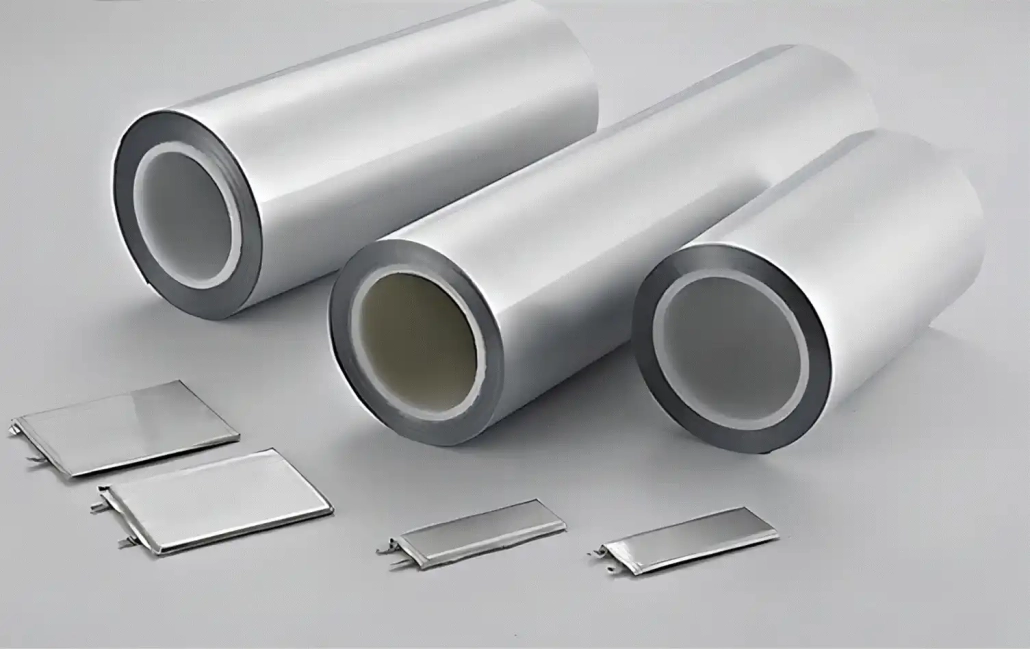